Boundary Layer & Subsonic Wind Tunnel (BLAST)
The Boundary Layer and Subsonic wind Tunnel (BLAST) was commissioned in July 2018. This facility consists of two test sections, one for reproducing high Reynolds number, boundary layer flows and a second test section for subsonic aeronautical applications. The first test section 30 m x 2.8 m x 2.1 m (L x W x H) enables a maximum velocity of 34 m/s with a minimum turbulence level of 0.1%. The side walls and ceiling are made of optical glass to provide optical access for flow visualizations or any laser-based measurement technique. The subsonic test section 10 m x 2.1 m x 2.1 m (L x W x H) achieves a larger maximum velocity of 50 m/s.

BLAST Instrumentation
Wind tunnel instrumentation includes stereoscopic Particle Image Velocimetry (PIV), multi-component hot-wire anemometry, velocity measurements with multi-hole pressure probes, pressure measurements with pressure scanners and force measurements with multi-component balances.
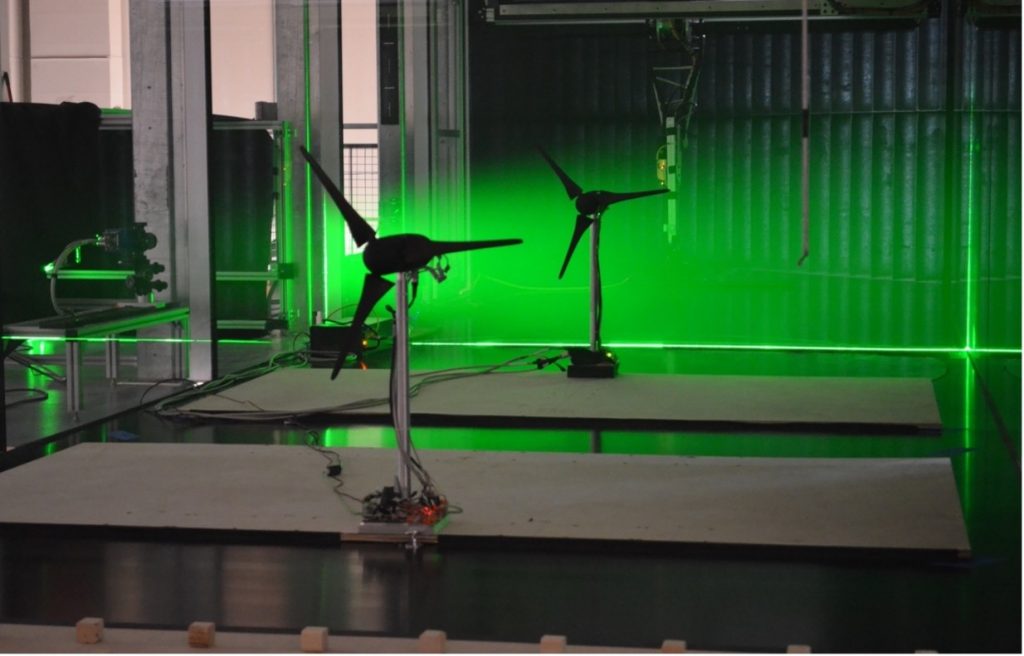
Wind-Wave Tunnel
The wind-wave tunnel is a large facility designed for air-sea interaction and marine renewable energy studies. The facility is central to their offshore wind energy research activities. The tank of the facility is roughly 15 m long with a working test section of about 13.5 m long, 1 m wide, and 1.8 m high. The entire test section is constructed from high-quality acrylic panels for optical measurements. The tank is equipped with a closed-loop wind tunnel capable of generating wind speeds up to 40 m/s. Further, the water tank is equipped with flap-type wavemakers, which allows for the generation of mechanical wave packets within the range of 0.8–1.5 Hz. Slow-moving currents can also be generated in the tank using a recirculating pump.

UTD Mobile LiDAR Station
This facility allows rapid deployment of two scanning Doppler wind LiDARs for probing the Atmospheric Boundary Layer (ABL), wind turbine wakes, and other environmental flows. The deployment of the wind LiDARs is performed through a truck and trailer devoted and equipped to perform field measurements.
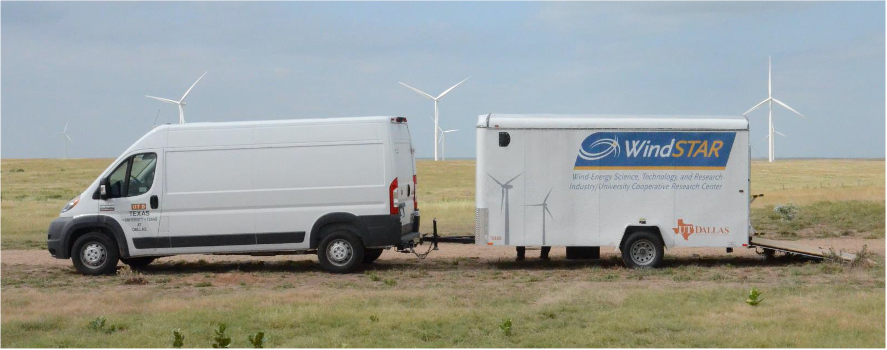
LiDAR Instrumentation
A WindCube 200S LiDAR by Leosphere and a Streamline LiDAR by Halo Photonics are connected to a workstation, which allows for remote control, monitoring, programming, and setup of the wind LiDARs. The remote-control unit includes a field computer with external hard-drive, modem for 4G network connection with two different providers, web-switch for power control of the unit itself and the two LiDARs, one datalogger CR3000 by Campbell scientific for data acquisition from atmospheric instruments, fans for temperature control of the unit, UPS and surge switch to prevent power shocks on the unit and LiDARs. Instrumentation to characterize atmospheric conditions is also available, such as sonic anemometers CSAT3 by Campbell Scientific, thermistors, one radiometer, and one LiCOR.

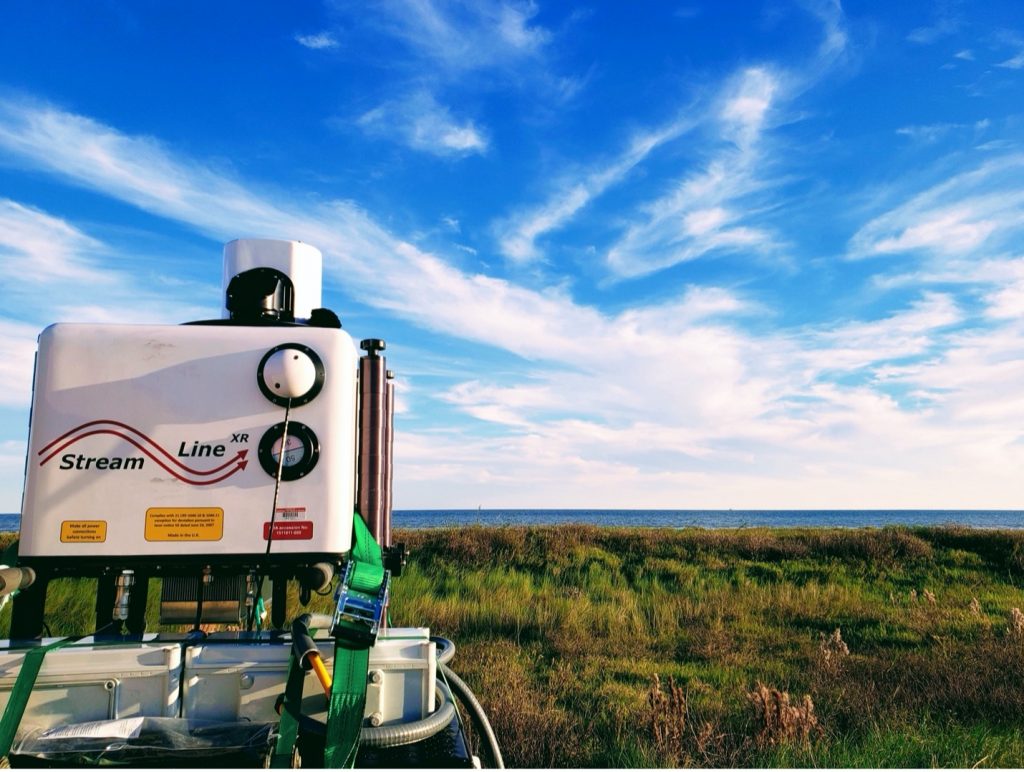
Structural Dynamics and Controls Lab
The Structural Dynamics and Controls lab focuses on gaining a better understanding of the dynamic behavior of structures and its control, developing new measurement techniques, and training students in experimental-based model validation methods. Dynamics measurement capabilities include modal testing, vibration measurement, and structural health monitoring. UTD Wind has the capability to test large structures in its Energy High-Bay lab with a floor space of 22m by 15m and a ceiling height of over 10m. Measurement systems include dynamic acceleration and strain, static strain, and non-contact 3D laser Doppler vibration (LDV) and displacement measurement.

Intelligent Energy Systems Lab
The Intelligent Energy Systems Lab provides an area for students and faculty to design, build and test intelligent systems for wind turbines and wind farms, which enhances the learning experiences and capabilities. The lab supports the development of mechatronics and electronics subsystems for research and education in wind turbines and wind farms. In this lab, researchers can perform circuit design, fabrication and testing necessary for diagnostics and control of wind turbine components. The computer workstations run software that supports numerical simulation and design of wind energy systems such as codes developed by NREL (e.g., WISDEM, OpenFAST, FLORIS, FAST.Farm, WindSE and others) as well as Matlab/Simulink, machine learning codes and productivity software.
